原子力システム研究開発事業及び原子力基礎基盤戦略研究イニシアティブ 成果報告会資料集
金属燃料の溶融電解精製における陰極・陽極の処理に関する研究開発
(研究代表者)飯塚政利 原子力技術研究所次世代サイクル領域 上席研究員
(再委託先)国立大学法人 豊橋技術科学大学
(研究開発期間)平成19年度〜21年度
1.研究開発の背景とねらい
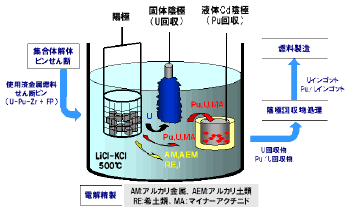
図1 電解精製工程の概念図
経済性、安全性、核拡散抵抗性に優れた核燃料サイクル技術の一候補として、U-Pu-Zrなどの合金を燃料とする金属燃料高速炉、溶融塩化物/液体金属溶媒を用いる乾式再処理、簡便な射出鋳造による燃料成型からなる金属燃料サイクルが注目されている[1]。乾式再処理の中心となる溶融塩化物浴中における電解精製工程では、せん断された使用済金属燃料を陽極溶解し、核分裂生成元素(以下FP)を取り除き、大半のUを金属製固体陰極の表面に、Puおよびマイナーアクチニドは液体Cd中にUと共に、それぞれ回収する(図1)。U回収については、工学規模試験により実用化に十分な速度が達成できることが確認されているが[2]、電解精製を使用済燃料からアクチニドを回収してリサイクル燃料原料とし、かつ核分裂生成物を分離廃棄する工程として捉えると、次のような課題が残っている。
(1)陽極残留物処理技術の開発
・電解精製終了後に陽極残留物中に少量残るアクチニド回収プロセスの開発
・SUS被覆管、Zr、貴金属FPからなる陽極残留物を主体とする金属廃棄物処理プロセスの開発
(2)陰極回収物処理技術の開発
・Zrが混入することにより融点が上昇したU回収物の均一インゴット化
・高温の溶融U-Zr合金/塩化物との両立性をもつ蒸留るつぼ材料の開発、及び実用機器設計
そこで本事業では、実際にU電解試験で生じた陽極残留物と陰極回収物、および模擬混合物を用いた高温蒸留試験などを通じてこれらの技術開発を実施した。さらに、U回収率と回収速度を高いレベルで両立するための運転条件を定め、これを基に乾式再処理プロセスにおけるマスバランス、回収率などの性能を評価した。
2.研究開発成果
2.1 陽極残留物の処理技術開発
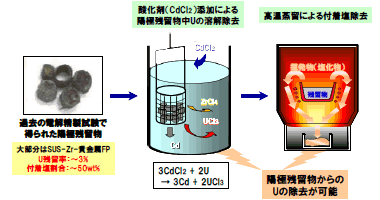
図2 本事業で提案した陽極残留物処理フロー
本事業では、塩化カドミウム(CdCl2)添加によるU溶解除去→付着塩化物蒸留除去という2つの工程を経た陽極残留物を溶融固化し、回収したアクチニドを塩化物として再処理プロセスに戻すことを提案した(図2)。
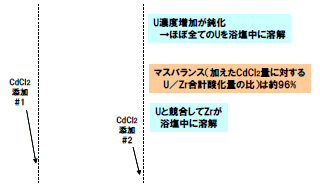
図3 U-Zr陽極溶解残留物からのU溶解除去試験における溶融塩中U、Zr、Cd濃度の変化
2.1.1 U-Zr陽極溶解残留物からのU溶解除去試験
過去にU-Zr合金を用いて行われた電解精製試験[2]で発生した陽極溶解残留物を対象として、CdCl2添加により未溶解Uを500℃のLiCl-KCl溶融塩中に溶解させる試験を行った(図2中央)。溶融塩浴中U、Zr濃度変化から、2日間程度以下でU溶解反応が完了し、処理速度の観点から乾
図1電解精製工程の概念図過去の電解精製試験で得られた陽極残留物3CdCl2+ 2U→3Cd + 2UCl3酸化剤(CdCl2)添加による陽極残留物中Uの溶解除去揮発物(塩化物)残留物高温蒸留による付着塩除去陽極残留物からのUの除去が可能大部分はSUS-Zr-貴金属FPU残留率:〜3%付着塩割合:〜50wt%図2本事業で提案した陽極残留物処理フロー
式再処理プロセスへの適用性が十分にあることがわかった(図3)。酸化反応におけるマスバランス試験全体を通じて良好であった。これらの挙動は、陽極残留物中の模擬FP(Mo、Pd)の有無に影響されなかった。模擬FPは電解精製とU溶解除去を経てもほぼ全量が陽極残留物中に留まった。
2.1.2 U溶解除去後の陽極残留物からの付着塩除去試験
2.1.1で未溶解Uを溶解除去した後の陽極残留物を対象として、高温蒸留によりUCl3を含む付着塩化物を除去する試験を実施した(図2右)。試験は、約600〜700℃で付着塩化物の溶融、約1200℃で塩化物揮発除去、約1400〜1500℃で残った陽極残留物(金属廃棄物)の溶融操作模擬、という温度制御パターンで実施した。塩化物揮発時には300Pa程度以下となるように必要に応じて装置内を減圧制御し、U-Zr合金溶融時には除去された塩化物の再揮発を防ぐためにArガスを導入して50kPa程度まで昇圧した。蒸留により陽極残留物中塩化物のほとんどが除去され、残留塩素濃度は最大で数千ppm程度であった。
市販ZrO2コーティングを施したグラファイト製るつぼ(Gr/ ZrO2、以下同様)、およびタングステン/ZrO2/ZrN(二層コーティング)については陽極残留物と反応した様子が見られなかったが、今後はより高温条件で溶融した陽極残留物に対するるつぼ材料の耐久性を検証することが必要である。試験後の陽極残留物分析結果から求めたU残留量から、電解精製と一連の陽極残留物処理とを通したU残留率を評価したところ0.04〜0.20%程度となり、模擬FPの有無による影響は見られなかった。この値は乾式再処理プロセス設計仕様であるU回収率99.5%を考慮しても十分に低い値である。
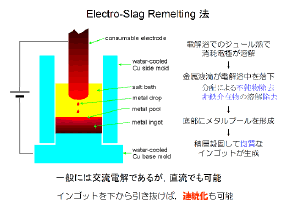
図4 ESR法の概念
2.1.3 陽極残留物からのアクチニド除去工程への高温金属再溶解法の適用性検討
CaF2-CaO等のスラグ中で鉄鋼およびSUS鋼を用いたエレクトロスラグ再溶解(ESR−図4)試験を行い、模擬アクチニド元素(Si、Ce)除去効果を調べた。その結果、Siについては製品インゴット中濃度が原料鋼中の半分程度に、Uと同程度の酸化物生成自由エネルギー変化を持つCeについては最高1/20程度にまでそれぞれ減少した。U等のアクチニドの酸化物生成自由エネルギー変化がCeと同程度であることを考慮すると、これらの元素もDC-ESR法による再溶解で除去可能であると期待される。したがって、ヒューム発生による周囲の汚染が少ないという特長と相俟って、ESR溶解は放射性廃棄物となったSUS鋼の処理に適用できる可能性を有していると考えられる。
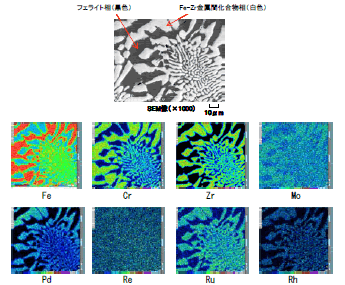
図5 溶融固化試料断面の元素分布測定結果
2.1.4 アクチニド除去後の陽極残留物の溶融固化試験
アクチニドを除去した後の陽極残留物に残るのは被覆管材料であるフェライト系SUS、燃料合金成分であるZr、貴金属FPである。これらは耐腐食性の高い金属であることから、溶融固化することにより安定な廃棄物形態とすることができると予測される。そこで、金属廃棄物の主成分となるSUSとZrとからなる混合物、あるいはこれに模擬貴金属FP(Mo、Ru、Rh、Pd、Re-Tc99模
図3U-Zr陽極溶解残留物からのU溶解除去試験における溶融塩中U、Zr、Cd濃度の変化CdCl2添加#1CdCl2添加#2U濃度増加が鈍化→ほぼ全てのUを浴塩中に溶解Uと競合してZrが浴塩中に溶解マスバランス(加えたCdCl2量に対するU/Zr合計酸化量の比)は約96%図4ESR法の概念
擬)を加えた混合物を対象とする溶融固化試験を実施した。その結果、1600℃以上の溶融温度、4kPa以上の圧力、Zr濃度5〜20wt%、使用済燃料中における対Zr比を超えない程度の貴金属FP濃度、という条件下で緻密で均一性の高い固化体が得られることがわかった。固化体はフェライト(Fe-Cr)相と金属間化合物相が細かく入り組んだ微小構造を持っており、模擬FP元素のうちPd, Ru, Rhが金属間化合物相に多く分布し、MoとReは両相に分布した(図5)。溶融金属のみを対象とする場合には、溶融金属との化学的両立性の観点からるつぼ材としてY2O3が最も好ましく、熱衝撃への耐性の観点からはAl2O3 (SSA-S)が適用できる可能性があることがわかった。
SUS-Zr-模擬FP合金溶融固化試験で作成された固化体試料を対象とした浸出試験を実施した。試料毎に結果のばらつきがあるものの、各元素の浸出量はガラス固化体に関する規格化浸出量と比較して1桁近く小さい値であり、廃棄物固化体の性能としては全く問題の無いものであることがわかった。
2.2 陰極析出物の処理技術開発
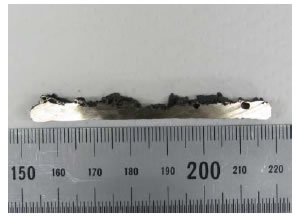
図6 U-Zr陰極回収物の高温蒸留処理試験で得られたU-Zrインゴット断面
2.2.1 U-Zr陰極回収物の高温蒸留処理試験
陰極回収物付着塩化物の揮発除去、U-Zrインゴット化に必要な運転条件を確認するため、過去に行われた電解精製試験で得られたU-Zr固体陰極回収物を対象とした蒸留試験を実施した。約600〜700℃で付着塩化物の溶融、約1000〜1200℃で塩化物揮発除去、約1400℃でU-Zr合金溶融、という温度制御パターンで蒸留試験を実施した。圧力制御は前述のU溶解除去後の陽極残留物からの付着塩除去試験と同様である。試験の結果、十分に凝集したU-Zrインゴットが得られた(図6)。内部の残留塩素濃度は数百ppm程度であり、ほぼ全ての塩化物が除去された。最もZr含有率が高い試料インゴット内には細かなZr-rich相が析出したが、マクロにはZr濃度の大きな偏りは見られず、乾式再処理工程管理を行う上で十分に均一であることが確認できた。
Gr/ ZrO2、タングステン/ZrO2、タングステン/ZrO2/ZrN(二層コーティング)について、蒸留るつぼ材料として適用性が期待できることがわかった。特にZrO2コーティングとして、市販のZrO2ビーズとZrO2粉末を混合して300μm程度以上の厚さに塗布・焼結したものは、るつぼ母材と内容物との反応抑制効果が高いだけでなく、使用後にU-Zrインゴットおよびるつぼ母材の両方から簡単に剥がすことができるため、インゴット取り出しとるつぼへのコーティング材再塗布の容易さの観点から最も適用性が高いと評価した。
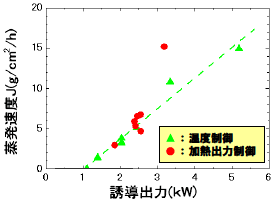
図7 工学規模蒸留試験における加熱誘導出力と蒸発速度との関係
2.2.2 工学規模蒸留試験
U換算で1kg/バッチ程度の工学規模蒸留装置を用いた塩化物揮発試験により、蒸留温度や誘導出力と蒸発速度との関係、回収に適した蒸発速度や加熱制御方法など、実用規模蒸留装置の設計要因として重要な知見を得た(図7)。これらを反映した適切な条件下における試験では、実用装置としての設計が十分成立する蒸留速度(15g/cm2/h)が得られた。回収された塩は嵩密度が小さく形状が一定でないが、再溶融・インゴット化することにより、電解精製装置への輸送に適した形態にすることができた。陰極析出物を模擬したペレット状銅金属とLiCl-KCl共晶塩を用い、蒸留による塩化物除去および金属溶融を連続して実施した結果、銅、塩ともにほぼ100%が高い純度で所定位置に回収されたことから、本事業で定めた運転条件により、陰極析出物からの付着塩塩化物除去ができる見込を得た。
2.3 陰極析出物/陽極残留物処理を含めた乾式再処理プロセスの構築
CdCl2添加によるU溶解除去工程で発生する浴塩を戻す先の工程としてはドロス処理工程[3](射出鋳造るつぼ/モールド、およびこれらに施すコーティング材とU金属との反応により発生するUO2などを、ZrCl4と反応させることにより塩化物に転換する)が最も適切であり、陰極処理工程で発生する回収塩化物は、量的な必要性に応じてドロス処理工程に送り、それ以外は直接電解精製工程に戻すのが適切であると評価した。
この検討に基づいて従来の乾式再処理プロセスフローに変更を加え、マスバランス検討を行ったところ、電解精製工程における陽極中ウラン残留率が一定値(例えば、ブランケットなし炉心、燃焼度150GWd/t、使用済燃料からのボンドNa蒸留除去実施、などの仮定下で6.8%)を超えると陽極処理で必要となるCdCl2持込み量が増え、プロセス全体における塩化物総量増大、ひいては塩廃棄物量の増加に繋がることがわかった。この範囲内であれば、トータルのUの出入量、使用済塩処理/塩廃棄物処理工程で処理すべき塩化物量、アクチニド回収率は変化しない。過去に行われた電解精製試験では陽極中ウラン残留率を20%程度から3%程度にまで低下させるのに数倍の時間を要したこと[2]を考慮すると、ある程度の陽極中ウラン残留率を許容し、陽極残留物処理を行うことにより電解精製処理時間が大幅に短縮されると予測されるが、この効果を定量的に評価するためには現状の試験データは不十分である。
3.今後の展望
本事業では、固体状態で取り扱われる核燃料物質量が多いバッチ処理プロセスであることに起因する計量管理の難しさ、廃棄物発生体積の増加、高温プロセスに適用できる材料・取扱技術の問題、研究開発実績の少なさからくる不確定要素の大きさなどの乾式再処理技術について指摘される技術的課題に応える多くの成果を挙げることができた。実用技術を目指す上で今後解決すべき課題として、溶融金属に対してより高い化学的両立性を持ち、容易に厚い皮膜を作成することが可能なコーティング材の開発、実際のU-Zr電解精製試験で発生した陽極残留物からの金属廃棄物固化体試料の作成と耐浸出性などの性能評価、固化体性能評価と処分シナリオに重大な影響を与える元素(99Tcなど)の挙動評価、が挙げられる。
4.参考文献
[1] “Assessment of advanced technologies for the future nuclear fuel cycle,” Proc. Int. Conf. on Future Nuclear Systems (Global’99), Aug. 29-Sep. 3, Jackson Hole, WY (1999).
[2] “Development of an innovative electrorefiner for high uranium recovery rate from metal fast reactor fuels”, J. Nucl. Sci. Technol., 46, 699?716 (2009).
[3] 日本原子力研究開発機構、「高速増殖炉サイクルの実用化戦略調査研究フェーズⅡ技術検討書 (2)燃料サイクルシステム」、JAEA-Research 2006-043 (2006).